
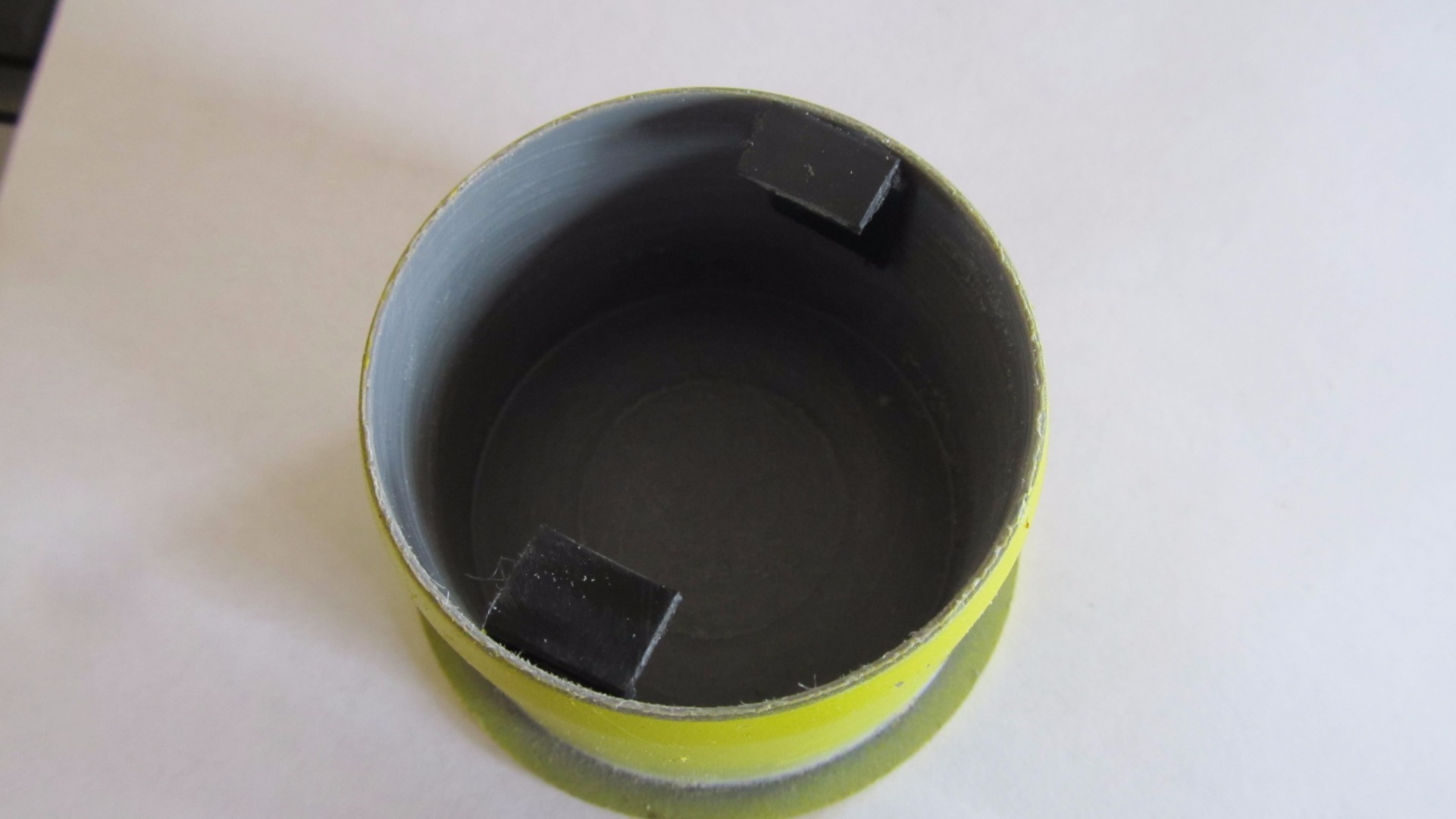
Serial kinematic designs have advantages when it comes to cost and simplicity, and work very well for most standard applications. In a multi-axis serial kinematics system, each actuator (and usually each sensor) is assigned to exactly one degree of freedom. Serial Kinematics for Lower Cost / Standard Applications They are vacuum compatible, operate over a wide temperature range, and require neither lubricants nor compressed air for operation.
PIEZOELECTRIC BUTTON FREE
Flexures are maintenance free and not subject to wear. Friction and stiction are entirely eliminated, and flexures exhibit high stiffness, load capacity, and resistance to shock and vibration. With the use of flexure guides and mechanical levers, the motion of a piezo stack can be multiplied (up to 100’s of microns or even a few mm) and guided at the same time. Flexure motion is based on the elastic deformation (flexing) of a solid material.

They typically consist of one or more of piezo elements driving a runner. Piezoelectric motors require more complex drive electronics and can provide long travel ranges (up to 100’s of mm). They provide short travel ranges typically under 1mm. Traditional piezo actuators expand analogous to the applied drive voltage. Piezo motion devices are often divided into two groups: actuators and motors. Email our engineers if you have additional questions about using PI piezo motion products to solve your application problem. This tutorial includes an introduction to the piezoelectric effect, a discussion of the difference bewtween a piezo actuator and a piezo motors, an explanation of hybrid mechanisms, and a quick start guide to PI piezo motion products. Close contact between user and manufacturer is the best recipe for success.
PIEZOELECTRIC BUTTON FULL
PI provides a large variety of piezo actuator and piezo motor drive technologies, each one optimized for different parameters such as cost, precision, force, speed and size. To use the advantages of piezoelectric positioning technology to its full extent, it is important to carefully analyze the application in which a piezo drive or nano-positioning system is to be used. There is not one single type of piezo drive that works for every application. The demand for higher speed and/or precision in fields such as bio-nanotechnology, semiconductors, metrology, data comm, and photonics keep pushing manufacturers to come up with innovative drive technologies.
